

In DAVE this is beautifully implemented using the “buoyancy-shape” node. This depends only on the shape of the hull of the vessel. This is simply the water that the vessel displaces when there are no waves. The simple solution is to keep fluid and structure separate, which is exactly what we will do. But when a vessel is composed of multiple parts this combination is very troublesome. Here G is the gravity acting on the vessel and M is the metacenter, a point derived from linearizing the horizontal displacement of the center of buoyancy due to vessel roll or pitch.Ĭombining fluid and structure is okay for simple vessels. Typically these two are combined, resulting in the familiar GM value. The static component due to the weight of the vessel as well as the static component due to the displaced fluid. Hydrostatics is the most tricky part as it comprises two components. Static fluid effects (Static pressure distribution) All actions are marked as:īut we will start with some theory to outline where we are going.įor a typical first order time-domain simulation involving floating bodies the following information is needed: But also for a simple vessel I recommend to use this method. In those situations the standard formulation of hydrostatic stiffness becomes extremely complicated. Especially if the vessel is composed of multiple elements such as cranes, cargo is placed on it or lifted from it or multiple vessels elements are interconnected. This may sound difficult but it actually makes many things a whole lot easier. It also introduces an alternative way of modeling the hydrostatics by removing the gravity effects from the stiffness matrix. This guide presents a step-by-step guide for setting up a vessel with first order diffraction data from orcawave. Setting up the vessels for such a model using orcaflex is easy but not trivial, but in the end it is just book-keeping. Journal of Ocean Engineering and Technology, 28(1), 85-92.Many offshore operations can be modeled using first order time domain analysis. Trend and Review of Corrosion Resistant Alloy (CRA) for Offshore Pipeline Engineering. Short-term course in GEM, Pohang University and Science and Technology, Pohang, Republic of Korea. Orcina Ltd., Daltongate, Ulverston, Cumbria. Altantia Offshore Ltd., Houston, TX, USA. Independence Hub - MC920 SCR Detailed Design: Riser Design Based & Methodology. MCS, Advanced Engineering Solutions, 2005. A Nontechnical Guide, 2nd Ed., PennWell, USA. Deepwater Petroleum: Exploration & Production. Leffler, W.L., Pattarozzi, R., Sterling, G., 2011. SCR Modelling and Analysis with a Deepwater Platform, Houston, TX, USA. Offhosre Standard F101, Det Norske Veritas, Oslo, Norway. Offshore Technology Conference, TX, USA.ĭet Norske Veritas (DNV), 2007. Characteristics of Ultra-deepwater Pipelay Analysis. API Bulletin 2INT-MET, American Petroleum Institute, Washington, USA.īai, Y., Bai, Q., 2005. Interim Guidance on Hurricane Conditions in the Gulf of Mexico. Recommended Practice 2RD, American Petroleum Institute, Washington, USA.Īmerican Petroleum Institute (API), 2007. Design of Risers for Floating Production Systems (FPSs) and Tension-leg Platforms (TLPs). The weight of the SCR and internal contents affected the maximum stress of the SCR more than the HOA and vertical soil stiffness, because the weight of the SCR, including the internal contents, was directly related to its tensile stress.Īmerican Petroleum Institute (API), 1998. Furthermore, the tensile stress governed the total stress of the SCRs, whereas the bending stress governed the total stress at the TDZ. Based on a deepwater SCR design example, it was found that the maximum stress of an SCR occurred at a hang-off location under parallel loading direction with respect to the riser plane, except for a wave dominant dynamic survival loading condition. The structural behavior of a deepwater SCR under various environmental loading conditions was investigated, and a sensitivity analysis was conducted with respect to various parameters such as the SCR weight, weight of the internal contents, hang-off angle (HOA), and vertical soil stiffness. Thus, the objective of this study was to develop an overall analysis procedure for a deepwater SCR. However, deepwater SCR analysis is a new research area.
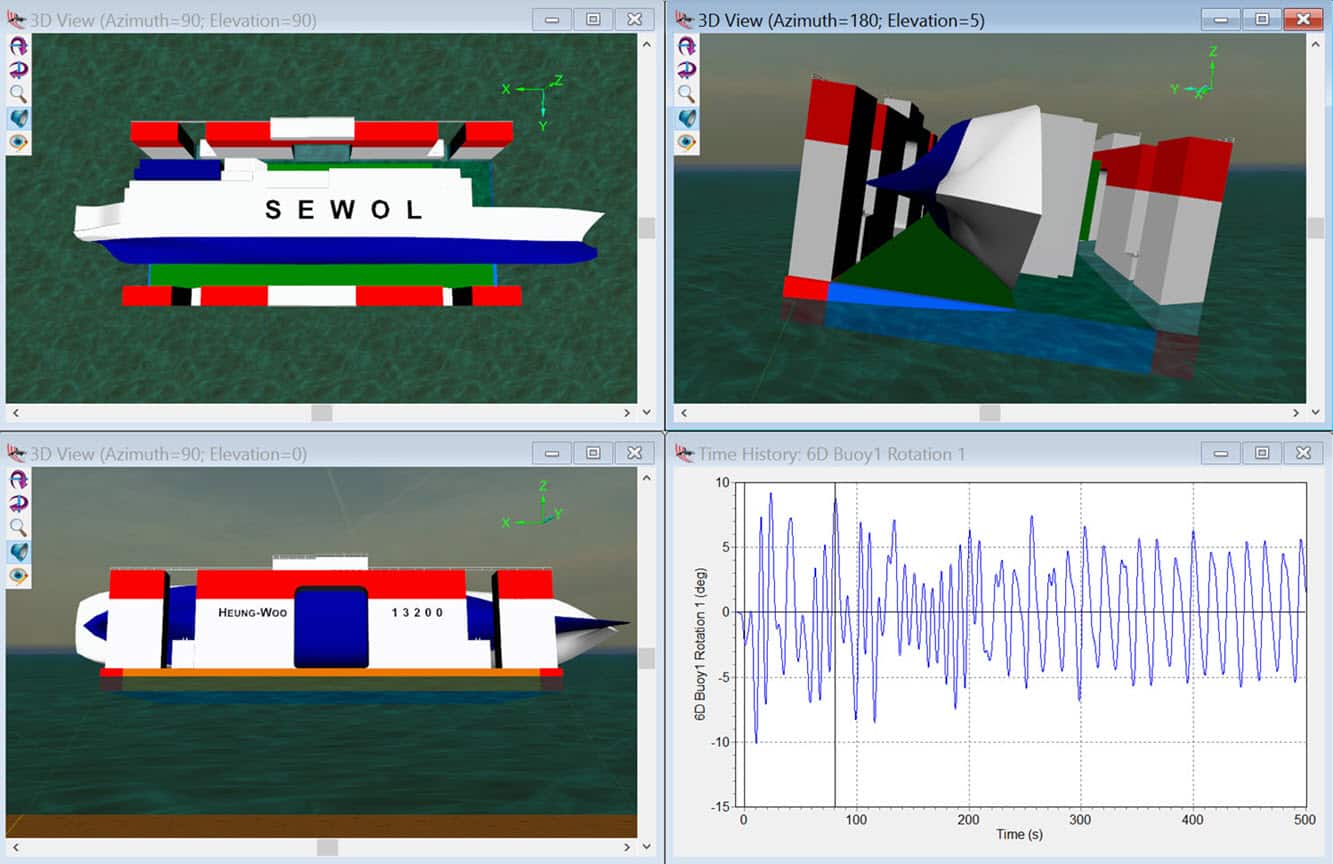
Therefore, a systematic strength analysis is required for the proper design of an SCR. The design challenges when attempting to obtain sufficient strength for a deepwater steel catenary riser (SCR) include high stress near the hang-off location, an elevated beam-column buckling load due to the effective compression in the touchdown zone (TDZ), and increased stress and low-cycle fatigue damage in the TDZ.
